Autonomous power supply centers for enterprises
Problems of industrial enterprises in the field of energy supply are known. This is limitation of capacity on the part of local power networks, excessive tariffs for heat and electricity, poor quality and reliability of energy supply. Cumulatively, they lead to "undue" capital and operational costs.
Therefore, calculating and provident industrialists, especially in energy-intensive industries, increasingly achieve high efficiency and competitiveness of their enterprises by creating their own enterprises autonomous power supply centers on the basis of GTU-TPP (GTU-CHPP), CCGT, GTPP or GRPP.
The use of cogeneration, steam-gas or trigeneration technologies provides production and process needs of enterprises with the necessary volumes of electricity, hot water, steam and cold.
The main purposes of creating autonomous power supply centers:
- guaranteed coverage of electrical loads in conditions of network restrictions;
- generation of own thermal capacity for various facilities of the enterprise;
- ensuring the process needs of production in hot water, steam and cold;
- significant reduction of energy consumption costs;
- reduction of the company's dependence on the tariff policy in the electricity market.
The investment attractiveness of these projects is also conditioned by full control by the owner-consumer.
As a result, own generating capacities allow the leaders of industrial business to achieve energy and financial efficiency, increase in profitability of production and competitiveness of the products.
It has been proven by industrial practice that autonomous power supply centers have a number of advantages, among which:
- high efficiency (when working in various combined cycles, the efficiency reaches 90%);
- low cost of generated electricity and heat (two and more times lower than network tariffs);
- short payback period (about 5 years - for electricity generation without heat recovery, up to 2-3 years - with complete heat recovery);
- possibility to connect additional power units with increasing needs of the enterprise;
- minimum commissioning time.
It is significant that in many fields autonomous power supply complexes are also being built and successfully functioning, where, as a rule, the associated petroleum gas produced just here is used as fuel.
The whole range of gas treatment equipment for autonomous power supply centers is offered by the ENERGAS Group of Companies. First of all - modular units for treatment and compression of fuel gas.
At the same time, the main process task is solved - provision of generating units with high-quality gas in accordance with set parameters for purity, temperature, pressure and flow.
These reasonable design requirements are made by the creators of modern gas turbine and combined-cycle power units to gas treatment equipment. After all, professionals are well aware of the direct dependence of achievement of design efficiency rate, reliability level and planned efficiency of turbines on the quality of gas fuel. Proceeding from this, ENERGAS specialists constantly care about the introduction of optimal engineering solutions in the procedure of complex gas treatment.
At present, ENERGAS equipment successfully operates as a part of ten autonomous power supply centers for industrial enterprises (without taking into account the power centers of the field's own needs).
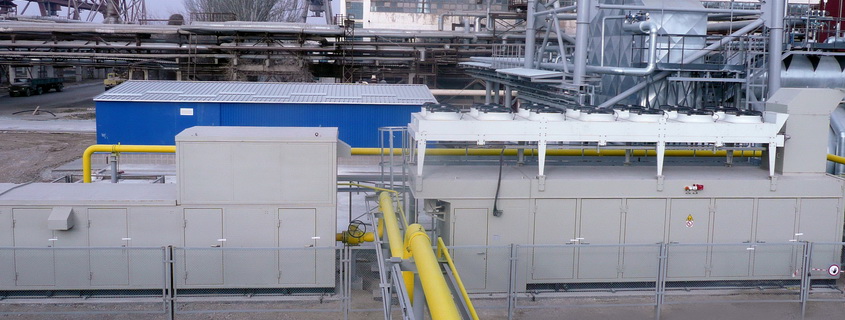
EXAMPLE OF THE PROJECT IMPLEMENTATION
The research and production complex "Angstrem-T" JSC is equipped with its own power supply center - an autonomous gas reciprocating power plant (GRPP), which operates on a trigeneration cycle and provides the company with the necessary volumes of electricity, heat and cold.
The design electric power of GRPP is 36 MW. The plant is based on five gas reciprocating units Wartsila 16V34DF with a capacity of 7 MW. Bifuel GRUs can run on gas and diesel fuel.
If necessary, switching between energy carriers occurs automatically, without stopping and reducing the load. Environmental standards of the power plant comply with all modern standards.
There is also a new boiler house in the building of the GRPP; it includes four Buderus Logano S825L hot water boilers complete with Saacke combined industrial block burners.
Gas fuel for GRPP and boiler comes through the multifunctional gas treatment system (GTS) of ENERGAS, which provides the necessary design parameters for purity, temperature, pressure and flow. GTS includes the following process equipment:
- unit of inlet gas filters for gas pretreatment;
- gas metering station for measuring fuel flow;
- separation system (two-stage filters-scrubbers) for fine gas purification;
- compressor station (two gas booster units) for fuel compression;
- in-site gas pipeline to the entrances to the buildings of the GRPP, FAB.
A step-by-step commissioning of the GTS, including erection supervision, commissioning, individual testing and integrated testing as part of the power plant, was carried out by the technical specialists of the company "ServicENERGAS".
At the same time, engineers of the ENERGAS Group carried out training of the customer's personnel on the rules and norms of equipment operation.
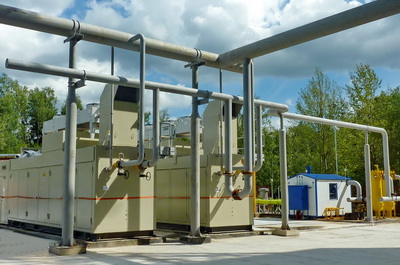